CEB Cabin Infrastructure 90% Complete
We hope you all had a Merry Christmas and will have a prosperous and Happy New Year!
We have been hard at work during November and December getting all the dirt work and infrastructure complete for the new Compressed Earth Block (CEB) cabin. We’ve trenched and installed the electrical conduit, water line, and septic tank connections. Now we are waiting for our electric company to install the meter and hook up the service side. At that point, we will have all utilities available to the new CEB Cabin. Unfortunately, I had forgotten to install the conduit for the internet. So that is still on the to-do list.
Here are some pictures of the work we have been doing.
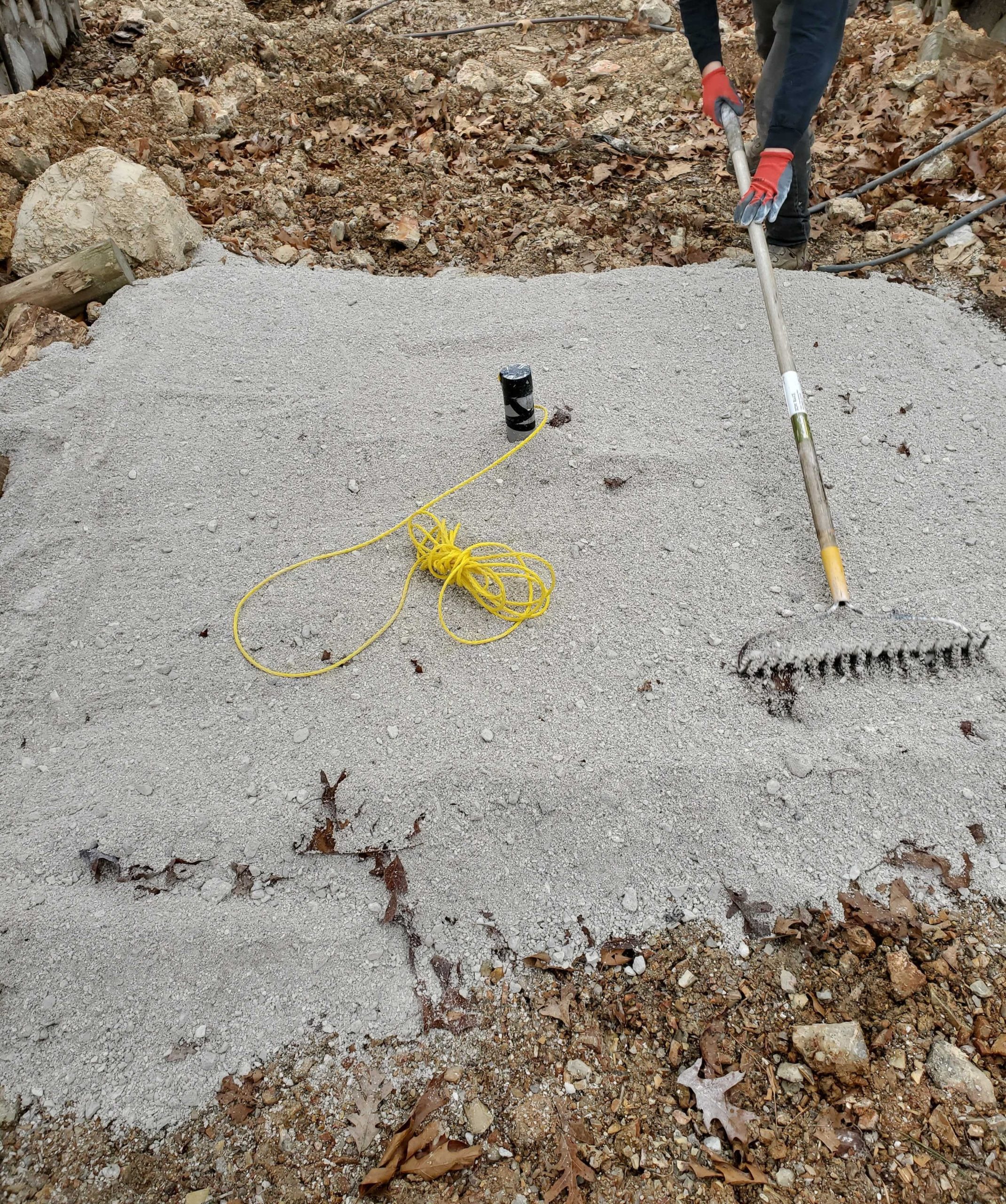
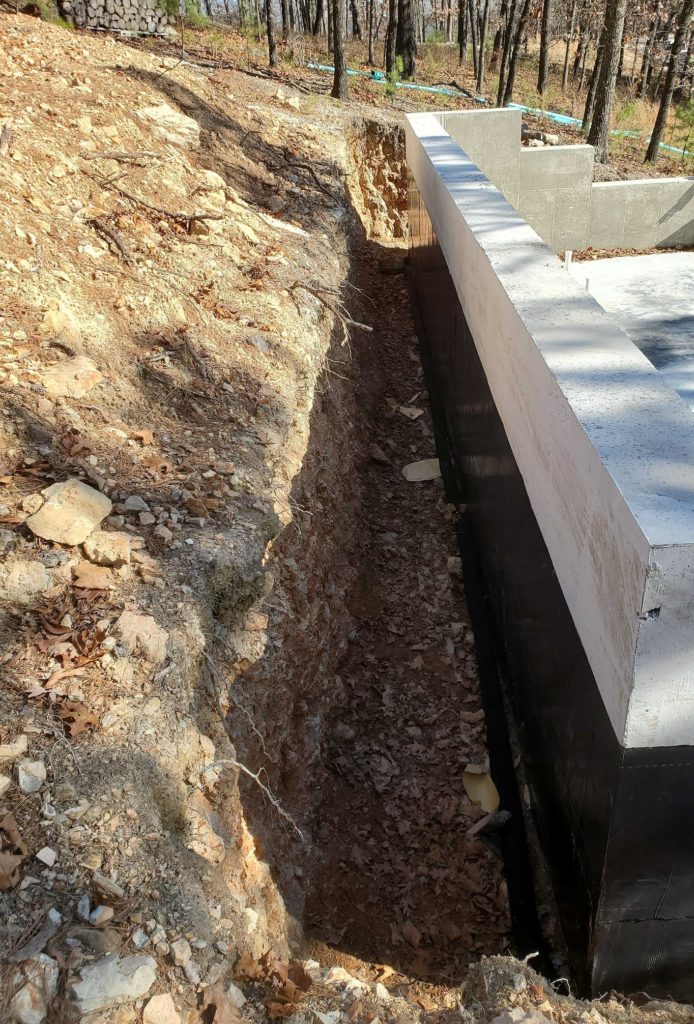
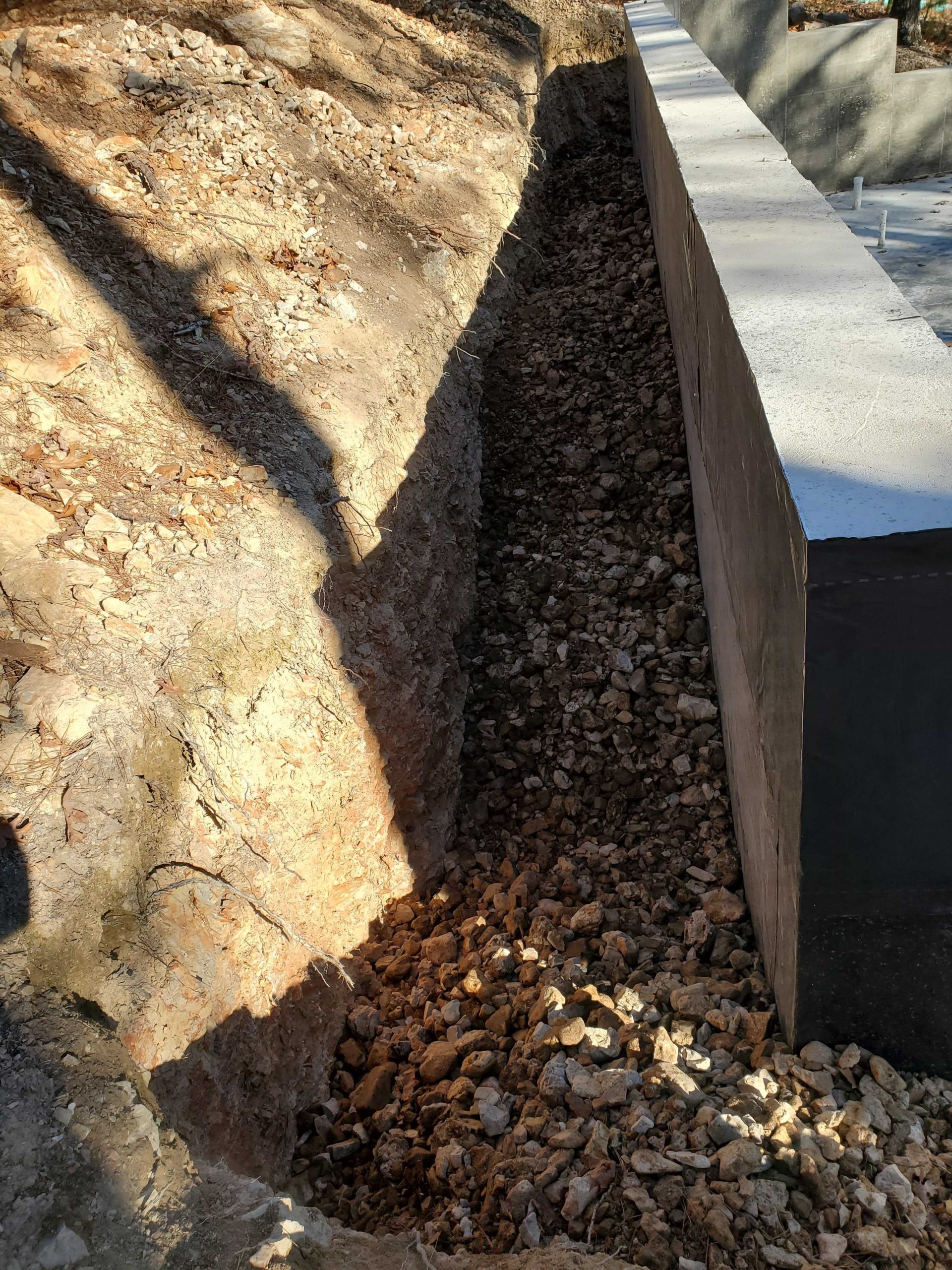
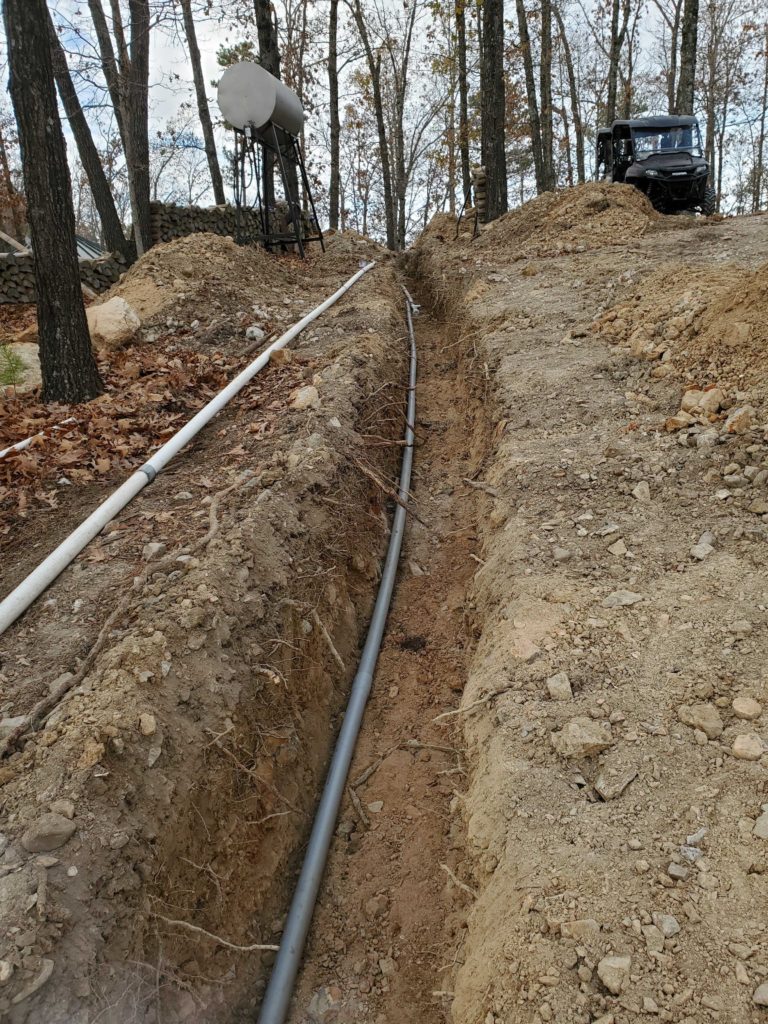
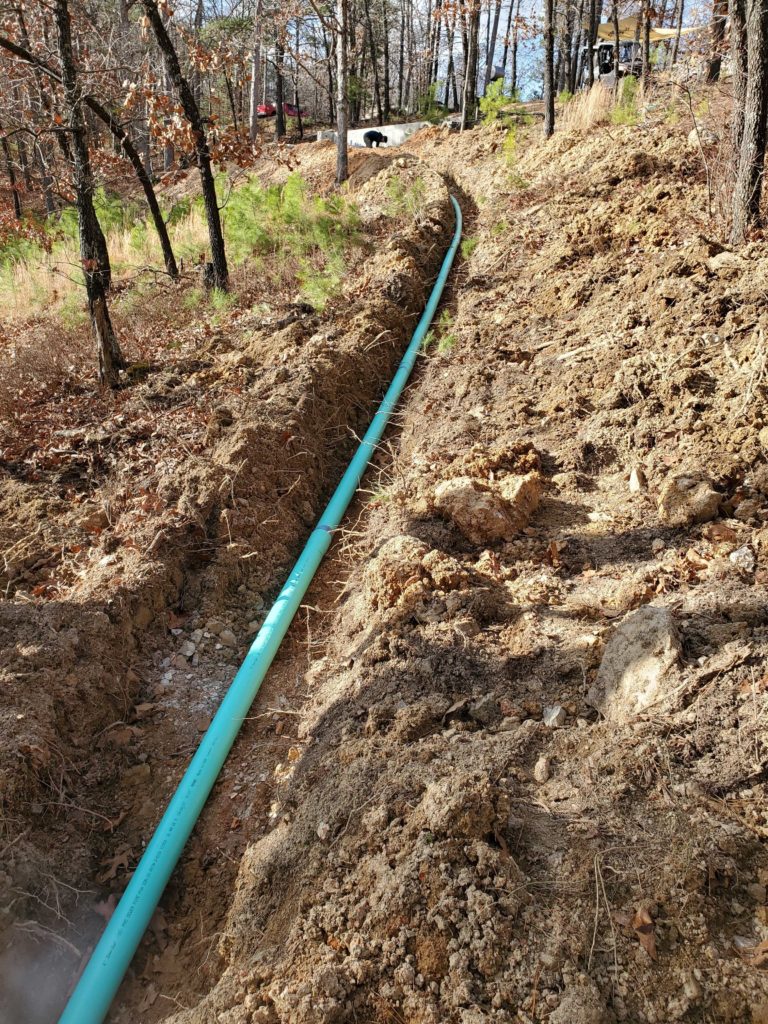
Testing Compressed Earth Block (CEB) Production
Compressed Earth Block Cabin Foundation is Complete
Groundbreaking for the Stabilized CEB Cabin
Finish out update
Dryed in, Finish-Out started
We now have the roof on. It was quite difficult because my harness was made to catch you in the event of a fall. The clip was designed to be in the back. Notice the belt on my back to hold the harness together. We had to retrofit it backwards so we could repel down the roof and pre-drill the holes and then screw it down. In order to do this you had to support your weight with one arm while you worked with the other.
Skylight installed. I only cut my forearm once on the edge of the roof getting it to the top. #superglue
Interior after sheet rock, texture, paint, and fixtures.
Interior looking over the deck to the view.
Kitchen, Bar area, and front door.
This is a sink I found for the bathroom. It carved out of a petrified wood tree log. It is stunning.
This a google earth photo of our property. The far left is our current house. In the middle is Yurt 1 (tarp on the roof) and bottom right is Yurt 2 (the one we are working to finish first). If you look real close you can see us working on the roof.
These are the materials that we have chosen for the finish out. Flat pebble rock shower floor, tile for the shower walls, bathroom and living room paint colors and high-end vinyl flooring (no grout lines and looks just as good as wood due to a lot of variations in the planks).
View from the road with the circular drive
Walkin shower rocked.
Dry in push continues
Final Push to Dry-In
Raise the ROOF!
Winter has arrived. And with it comes the inevitable construction delays.
After the wall were erected on Yurt 1, it was time to raise the Roof. First step was to calculate the height and positioning of the center compression ring. Once the calculations were complete, checked and rechecked, it was time to construct the stand on which the compression ring would sit. After it was build, Gator and I had to figure out how to get the stand on top of the scaffolding. After a couple failed plans and near drops or falls, we finally succeeded.
Next we had to get the compression ring on top of the 14′ 7″ stand. HUM? For this we had to bring in some additional muscle. Much like the stand, several attempts were made using a pulley system to no avail. So, we decided on trying to build a ramp from the top of the wall to the stand. After a couple hours, the Eagle had landed.
The next task was to secure the roof rafters from the top of the walls to the compression ring. Some slight modifications had to be made to the rafters before we could install. After several hours of tweaking we finally had the first four rafters up. Then came the rain.
We tarped the yurt with a 6 mil 50 x 50 tarp. No easy feat on a rocky slope, I will let you know. We though we had the tarp tight enough to slope the water off the roof, but upon inspection the next day we had huge areas on top of the roof holding massive amounts of water. The tarp grommets had pulled free on several of the tie-downs. So, it looked like we had built an awesome rain water collection system. After several hours I got the water siphoned off the tarp and we reinforced the tie-downs.
Then came the snow. The dogs loved it, the production schedule hated it. I was pressing to try and get the rafters up before the weather set in so we would work inside on the ceiling panels, but it did not happen.
That is the update. Next up is getting the rafters up on Yurt 2, building and installing 80 ceiling sections, wiring the interior, plumbing stubbed out, AC lines installed, and finally having the outer ceiling, interior walls and exterior floor spary foamed with insulation, and metal roofing installed.